AI and nano-3D printing produce breakthrough high-performance material
Nanoarchitected materials combine strength, lightweight design, and sustainability, revolutionizing aerospace, automotive, and defense industries.
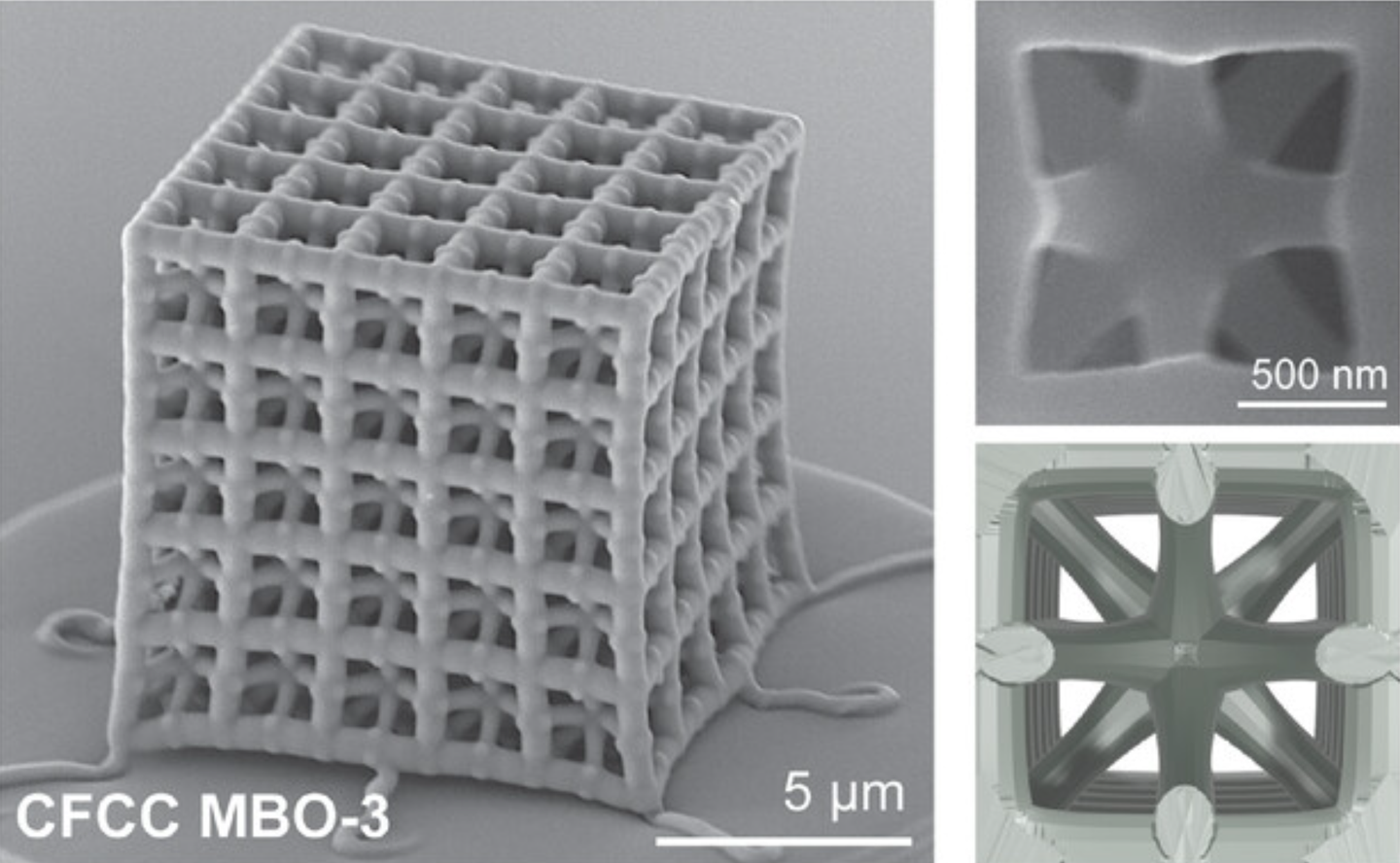
FESEM images of CFCC MBO-3 and Standard CFCC of equivalent density. (CREDIT: Advanced Materials)
Nanoarchitected materials represent a transformative leap in material science, combining strength, lightweight properties, and customizability like never before. These materials have achieved unparalleled specific strength, stiffness, and energy absorption, outpacing traditional materials used in industries like aerospace, defense, and optics.
The secret lies in their nanoscale design, which combines efficient geometries, high-performance materials, and nanoscale size effects to create structures that are both durable and lightweight.
Despite their remarkable potential, these materials face challenges, particularly in optimizing geometric performance and addressing stress concentrations that limit their durability.
For over a decade, researchers have explored various nanoarchitected geometries, including lattices, gyroids, and honeycombs. While some designs, like plate-lattice hybrids and shell triply periodic minimal surfaces, have improved stress distribution, they often rely on complex manufacturing processes and high relative densities.
Another limitation has been the performance of constituent materials. Pyrolytic carbon, for instance, offers impressive specific strength, nearing that of diamond, when confined to nanoscale dimensions. However, the atomic mechanisms underlying this strength remain poorly understood, hindering widespread adoption.
A groundbreaking solution has emerged through the integration of machine learning with advanced nanoscale manufacturing.
A team led by Professor Tobin Filleter at the University of Toronto, in collaboration with researchers from the Korea Advanced Institute of Science & Technology (KAIST), has developed a method to design and manufacture nanoarchitected materials with exceptional strength and lightweight properties.
Using a multi-objective Bayesian optimization (MBO) algorithm, they optimized the geometric performance of nanolattices. This approach allows for improved stress distribution and enhanced strength-to-weight ratios while minimizing density.
These advanced designs were brought to life using two-photon polymerization (2PP) nanoscale additive manufacturing. The process involved printing nanolattices with strut diameters as small as 300 to 600 nanometers.
Related Stories
These structures were then subjected to pyrolysis, a process that enhances the carbon purity and increases sp2 bonding, especially in the outer shell regions of the struts.
The result? Carbon nanolattices with compressive strengths comparable to carbon steel (180–360 MPa) and densities akin to Styrofoam (125–215 kg/m³). These materials exceed the specific strength of equivalent low-density materials by more than an order of magnitude.
Peter Serles, the first author of the study, highlighted the innovative use of machine learning in the design process. “Nanoarchitected materials combine high-performance shapes, like making a bridge out of triangles, at nanoscale sizes,” he explained. “However, standard lattice geometries tend to have sharp intersections that lead to stress concentrations and early failure. Machine learning was the perfect tool to tackle this challenge.”
The MBO algorithm used in this research required only 400 high-quality data points derived from finite element analysis, a stark contrast to the tens of thousands typically needed by other algorithms.
This efficiency enabled the prediction of entirely new lattice geometries, doubling the strength of existing designs. The optimized nanolattices withstood a stress of 2.03 MPa per cubic meter per kilogram of density, five times stronger than titanium.
This breakthrough holds significant promise for various industries, particularly aerospace and automotive. Professor Filleter emphasized the potential environmental impact of replacing heavier materials with these lightweight alternatives.
“Ultra-lightweight components in planes, helicopters, and spacecraft could reduce fuel demands while maintaining safety and performance. For instance, replacing titanium components on a plane with this material could save 80 liters of fuel per year for every kilogram replaced.”
The international collaboration behind this research highlights the multidisciplinary nature of the project. Researchers from Karlsruhe Institute of Technology (KIT) in Germany, the Massachusetts Institute of Technology (MIT), and Rice University in the United States contributed to the effort, alongside experts from the University of Toronto. This diverse team combined expertise in material science, machine learning, chemistry, and mechanics to achieve these groundbreaking results.
One of the most exciting aspects of this research is the scalability of these designs. Serles, now a Schmidt Science Fellow at Caltech, noted that future efforts will focus on scaling up these materials for cost-effective macroscale applications. This step is crucial for transitioning the technology from the lab to real-world applications.
The potential applications of these materials extend beyond aerospace. Their unique properties could benefit sectors ranging from automotive manufacturing to defense and energy. For instance, their high energy absorption characteristics make them ideal for impact protection, while their lightweight and strong structures could revolutionize the design of consumer products.
Despite these advances, challenges remain. Further research is needed to push material architectures to even lower densities without compromising strength and stiffness. Understanding the atomic mechanisms driving the performance of pyrolytic carbon at the nanoscale will also be essential for optimizing and expanding its use.
As this field continues to evolve, the integration of machine learning and advanced manufacturing techniques promises to redefine material science. By harnessing the power of data-driven design, researchers are opening new possibilities for creating materials that are not only stronger and lighter but also more sustainable.
The implications for industries worldwide are profound, offering a pathway to innovative solutions that could reduce environmental impact while enhancing performance.
Note: Materials provided above by The Brighter Side of News. Content may be edited for style and length.
Like these kind of feel good stories? Get The Brighter Side of News' newsletter.
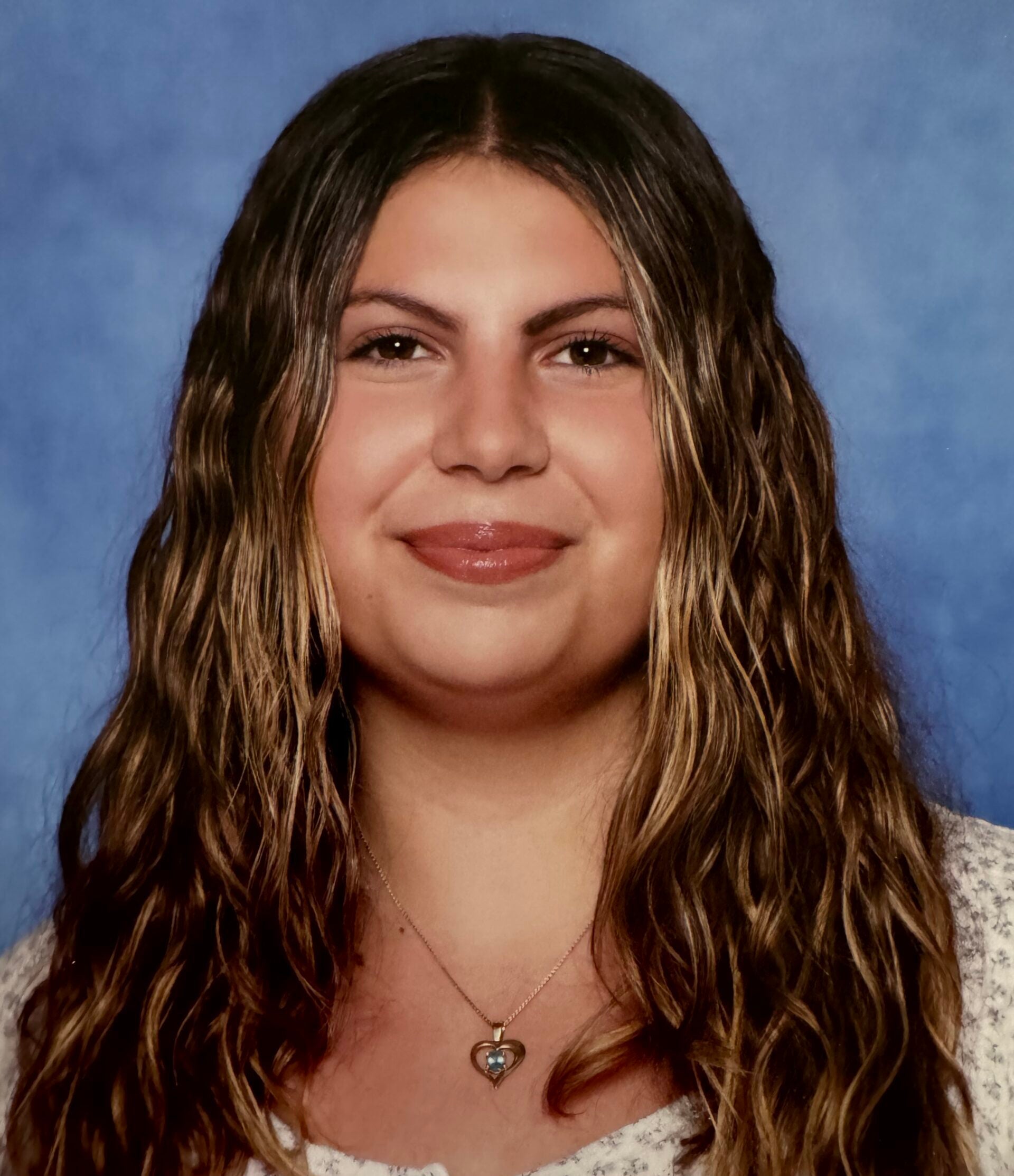
Rebecca Shavit
Science & Technology Journalist | Innovation Storyteller
Based in Los Angeles, Rebecca Shavit is a dedicated science and technology journalist who writes for The Brighter Side of News, an online publication committed to highlighting positive and transformative stories from around the world. With a passion for uncovering groundbreaking discoveries and innovations, she brings to light the scientific advancements shaping a better future. Her reporting spans a wide range of topics, from cutting-edge medical breakthroughs and artificial intelligence to green technology and space exploration. With a keen ability to translate complex concepts into engaging and accessible stories, she makes science and innovation relatable to a broad audience.