New Printing Process Advances 3D capabilities
Stronger parts for airplanes, automobiles, medical are just some of the products that could be created through a new 3D printing technology
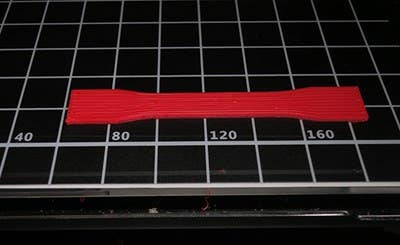
[July 31, 2020: UMass Lowell]
More durable prosthetics and medical devices for patients and stronger parts for airplanes and automobiles are just some of the products that could be created through a new 3D printing technology invented by a UMass Lowell researcher.
Substances such as plastics, metals and wax are used in 3D printers to make products and parts for larger items, as the practice has disrupted the prototyping and manufacturing fields. Products created through the 3D printing of plastics include everything from toys to drones. While the global market for 3D plastics printers is estimated at $4 billion and growing, challenges remain in ensuring the printers create objects that are produced quickly, retain their strength and accurately reflect the shape desired, according to UMass Lowell’s David Kazmer, a plastics engineering professor who led the research project.
Called injection printing, the technology Kazmer pioneered is featured in the academic journal Additive Manufacturing posted online last week.
The invention combines elements of 3D printing and injection molding, a technique through which objects are created by filling mold cavities with molten materials. The marriage of the two processes increases the production rate of 3D printing, while enhancing the strength and properties of the resulting products. The innovation typically produces objects about three times faster than conventional 3D printing, which means jobs that once took about nine hours now only take three, according to Kazmer, who lives in Georgetown.
Like these kind of stories? Get The Brighter Side of News' newsletter.
“The invention greatly improves the quality of the parts produced, making them fully dense with few cracks or voids, so they are much stronger. For technical applications, this is game-changing. The new process is also cost-effective because it can be used in existing 3D printers, with only new software to program the machine needed,” Kazmer said.
The process took about 18 months to develop. Austin Colon of Plymouth, a UMass Lowell Ph.D. candidate in plastics engineering, helped validate the technology alongside Kazmer, who teaches courses in product design, prototyping and process control, among other topics. He has filed for a patent on the new technology.
UMass Lowell is a national research university located on a high-energy campus in the heart of a global community. The university offers its more than 18,000 students bachelor’s, master’s and doctoral degrees in business, education, engineering, fine arts, health, humanities, sciences and social sciences. UMass Lowell delivers high-quality educational programs, vigorous hands-on learning and personal attention from leading faculty and staff, all of which prepare graduates to be leaders in their communities and around the globe. www.uml.edu
More information:
David O. Kazmer et al, Injection printing: additive molding via shell material extrusion and filling, Additive Manufacturing (2020). DOI: 10.1016/j.addma.2020.101469
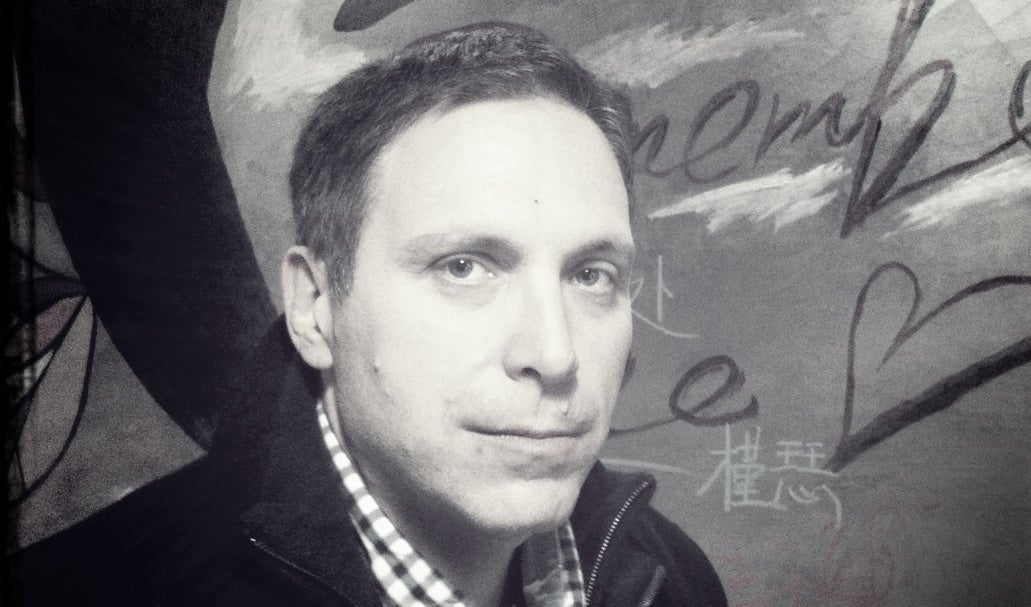
Joseph Shavit
Head Science News Writer | Communicating Innovation & Discovery
Based in Los Angeles, Joseph Shavit is an accomplished science journalist, head science news writer and co-founder at The Brighter Side of News, where he translates cutting-edge discoveries into compelling stories for a broad audience. With a strong background spanning science, business, product management, media leadership, and entrepreneurship, Joseph brings a unique perspective to science communication. His expertise allows him to uncover the intersection of technological advancements and market potential, shedding light on how groundbreaking research evolves into transformative products and industries.