Recyclable circuit boards may help solve the world’s growing e-waste crisis
Researchers create a recyclable, self-healing circuit board that could cut down on global e-waste.
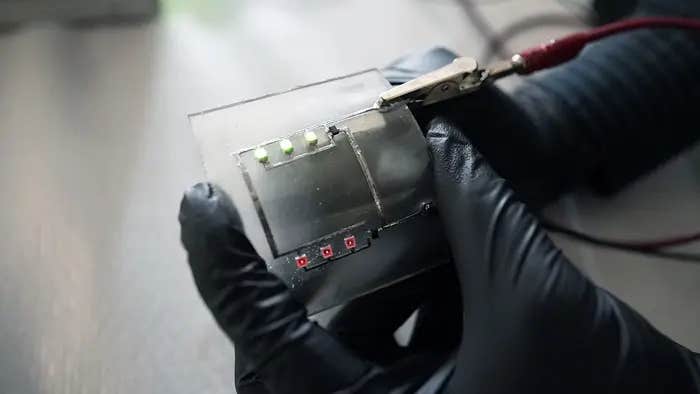
A new Virginia Tech material blends liquid metal with recyclable plastic to create self-healing circuit boards that could reduce e-waste. (CREDIT: Photo by Alex Parrish for Virginia Tech)
Every year, mountains of electronics are tossed into landfills. Broken phones, outdated laptops, worn-out tablets — the pile keeps growing. According to a 2024 report from the United Nations, the global total of electronic waste has nearly doubled in the last 12 years. It’s now up to 62 billion kilograms. That's roughly the weight of 1.55 million fully-loaded shipping trucks. And by 2030, it’s expected to jump to 82 billion kilograms.
Here’s the bigger issue: only 20 percent of that waste is recycled. That’s just 13.8 billion kilograms. The rest ends up buried or burned.
Electronics are made of many materials — plastic, metals, glass, and circuits — that are hard to separate. Standard recycling methods are expensive and energy-hungry. Worse, they lose a lot of valuable materials like gold and copper in the process. That means billions of dollars are literally going to waste.
But researchers at Virginia Tech may have found a solution. Published in the journal, Advanced Materials, a new material they’ve developed could transform how electronics are made and recycled.
The Science Behind a Smarter Circuit
Engineers and chemists at Virginia Tech teamed up to rethink what a circuit board can be. Traditionally, circuits are made from a type of plastic that becomes permanently hard once it's set. These “thermosets” are nearly impossible to break down, which makes recycling very difficult.
The new material is different. It starts with something called a vitrimer — a flexible plastic with special chemical bonds that can break and re-form when heated. This lets it be reshaped and reused, just like soft plastics, while still being strong and heat-resistant like hard plastics.
Related Stories
The team mixed this vitrimer with tiny droplets of a liquid metal made from gallium and indium. This metal stays in liquid form at room temperature and carries electricity as well as copper. By using a planetary mixer, the researchers were able to shear the liquid metal into microdroplets that spread throughout the plastic.
What’s special is how the liquid metal behaves inside the plastic. It settles into layers, forming a naturally conductive region in the material. The result is a strong, flexible, and electrically conductive composite that can be healed, reshaped, and reused over and over.
“Even under mechanical deformation or damage, the boards still work,” said Michael Bartlett, associate professor of mechanical engineering. “Our material is unlike conventional electronic composites.”
The circuits don’t just bounce back after damage. They can actually heal themselves. If scratched or torn, a little heat makes the plastic bonds re-link. The electricity keeps flowing, even after repairs.
Testing Its Strength
To confirm the material’s strength, researchers pushed it through rigorous tests. First, they checked how tightly the plastic chains were connected. They soaked it in five types of solvents, including methanol and acetone, to see how much it swelled. Most samples kept their shape, showing that the plastic was strongly cross-linked.
Then they heated it to 130°C — about the temperature of a home oven — and saw that it still held its form. It didn't start breaking down until 300°C, making it stable for most electronics use. Stress tests showed it could stretch and recover, with a tensile strength between 60 and 80 megapascals — similar to the plastics used in hard electronics today.
The team also tested how the plastic responded over time. At 170°C to 200°C, the material softened and could be reshaped. That’s because of the way its dynamic bonds respond to heat, allowing it to be molded again and again. Even after four remolding cycles under a press, the material held up.
What makes this even more impressive is that the whole process doesn’t require harsh chemicals or extreme heat. Most plastics with dynamic properties need a strong catalyst and temperatures near 180°C to cure. But this composite sets at just 40°C — barely above room temperature. That means easier, cheaper production.
A Smarter Path for Recycling
With this new composite, recycling electronics doesn’t have to mean waste and fire. Instead, the researchers showed that the material can be chemically broken down using a process called alkaline hydrolysis. This lets key components like LEDs and liquid metal be recovered cleanly.
“Traditional circuit boards are made from permanent thermosets that are incredibly difficult to recycle,” said Josh Worch, assistant professor of chemistry. “Here, our dynamic composite material can be healed or reshaped if damaged by applying heat, and the electrical performance will not suffer.”
That opens the door to a closed-loop system where entire circuit boards can be reused. No more melting down metals or grinding up fiberglass. Everything — from the flexible plastic to the wiring — could be salvaged and rebuilt.
And because the liquid metal forms on its own into conductive pathways, there’s no need to solder or glue parts together. In fact, the team demonstrated that a 1.5 mm thick sample of their composite could support 9 kg of weight while keeping an LED light on. That’s strong and smart.
Changing the Future of Electronics
Over the years, scientists have tried many ways to build flexible electronics. Some used brittle plastics, others added carbon nanotubes or graphene. But none offered the right mix of strength, conductivity, flexibility, and recyclability.
Earlier attempts with liquid metals focused on soft gels or stretchy rubber. Those materials worked for wearable devices, but not for strong, rigid electronics like phones or laptops. They also tended to wear out faster.
This new Virginia Tech material changes that. It blends the best features of past approaches — dynamic bonds, strong polymers, and liquid metals — into one single composite.
What’s more, it works at low metal concentrations. The team got full conductivity with as little as 5 percent liquid metal by volume. The droplets naturally formed into tight networks that allowed electricity to flow, even under pressure or stretching.
By layering these materials, the researchers could create entire circuit boards with built-in wiring and insulation — no need for multiple materials or manufacturing steps. That simplifies the design and makes recycling even easier.
While the material still needs testing in real-world electronics, its early results are promising. It's durable, adaptable, and built for reuse. If widely adopted, it could lead to electronics that don’t just break and get tossed, but get fixed and reborn.
The goal isn’t to stop people from buying new tech. Instead, it’s to make sure old devices don’t end up polluting the planet.
Note: The article above provided above by The Brighter Side of News.
Like these kind of feel good stories? Get The Brighter Side of News' newsletter.
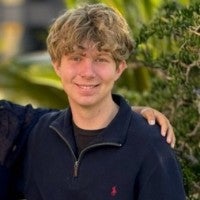
Joshua Shavit
Science & Technology Writer | AI and Robotics Reporter
Joshua Shavit is a Los Angeles-based science and technology writer with a passion for exploring the breakthroughs shaping the future. As a contributor to The Brighter Side of News, he focuses on positive and transformative advancements in AI, technology, physics, engineering, robotics and space science. Joshua is currently working towards a Bachelor of Science in Business Administration at the University of California, Berkeley. He combines his academic background with a talent for storytelling, making complex scientific discoveries engaging and accessible. His work highlights the innovators behind the ideas, bringing readers closer to the people driving progress.