School made from sugarcane waste signals a new era in sustainable construction
Sugarcrete transforms sugarcane waste into a green building material that could replace bricks and concrete while cutting carbon emissions by 80%.
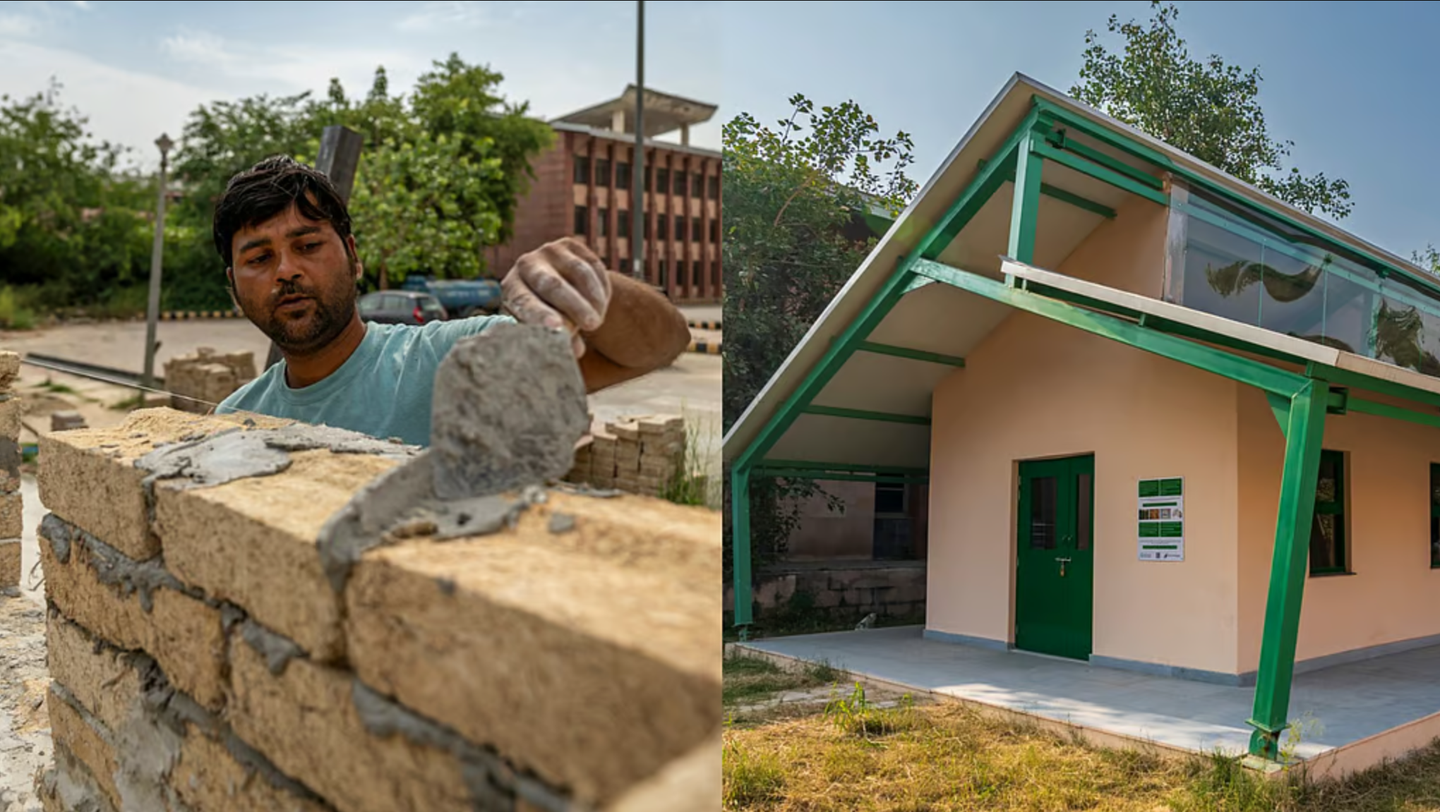
At Panchsheel Inter College in Uttar Pradesh, students are attending classes in a newly constructed school wing made not of concrete or standard brick, but of an innovative material derived from sugarcane. (CREDIT: UEL)
As the global climate crisis worsens, finding greener ways to build homes, schools, and cities has never been more urgent. One of the most promising breakthroughs is emerging from the University of East London’s Sustainability Research Institute, where a team has created Sugarcrete™ — a new building material that could change construction forever.
Working with Tate & Lyle Sugars, the team combined bagasse, the fibrous waste left after processing sugarcane, with special sand and mineral binders. What they produced isn’t just another eco-friendly idea. Sugarcrete™ could offer a way to build structures with a fraction of the carbon emissions of traditional materials.
Rethinking Construction Materials
The construction industry, long blamed for high carbon emissions, desperately needs alternatives. Concrete alone accounts for around 8% of global CO₂ emissions each year.
Sugarcrete™ steps in as a lighter, stronger, and greener solution. Compared to standard concrete, Sugarcrete™ cuts carbon use by 80 to 85%, requires only a week to cure instead of 28 days, and weighs just one-fourth to one-fifth as much.
Developers also say Sugarcrete™ costs much less to produce. That savings could make it attractive not only for rich cities, but also for fast-growing regions in the Global South where sustainable construction options are limited.
Armor Gutierrez Rivas, Senior Lecturer in Architecture at the University of East London, highlighted the enormous potential. "Sugarcane is the world’s largest crop by production volume – almost two billion tonnes produced worldwide yearly, yielding six hundred million tonnes of fibre bagasse as a by-product. With Sugarcrete™, the potential CO₂ savings are staggering, possibly mitigating up to 3% of the global CO₂ production," he explained.
Given that buildings and construction account for about 40% of annual global emissions, the innovation could have lasting impacts. As global floor areas are expected to double by 2060, new materials like Sugarcrete™ are essential.
Related Stories
Designing a New Way to Build
Using advanced digital modeling and robotic fabrication, researchers at East London designed a prototype Sugarcrete™ floor slab. Working closely with architects from Grimshaw, they developed an interlocking system based on a 17th-century dry assembly method by Abeille. This design transfers weight efficiently across the slab, allowing builders to use up to 90% less steel reinforcement.
Elena Shilova, an architect from Grimshaw, shared how the material’s properties give it extra benefits. “Sugarcrete™, when integrated as a floor slab, adapts Abeille’s 1699 design for dry assembly flat vaults. The interlocking components transfer loads across the slab, seeing a reduction in steel content by up to 90%," Shilova detailed.
Sugarcrete’s unique structure also helps it withstand seismic shocks. That feature is especially important in earthquake-prone regions where sugarcane grows in abundance. The different densities in sugarcane fibers absorb stresses that would normally crack conventional concrete, making structures safer.
Lab tests have also shown that Sugarcrete™ has strong fire resistance, excellent sound insulation, and high thermal performance. It meets or exceeds industrial standards, showing that it is not just greener, but also tougher than traditional options.
Real-World Testing Underway
To test Sugarcrete™ in real-world conditions, the University of East London partnered with Chemical Systems Technologies in India. Using local sugarcane waste, they set up the first production facility and worked with students from the Delhi School of Architecture and Planning.
The team’s first major project was at Panchsheel Inter College in Uttar Pradesh. There, a new school wing was built using Sugarcrete blocks instead of concrete or traditional bricks. The project served both as a construction experiment and a learning experience.
Alan Chandler, Associate of the Sustainability Research Institute and a co-creator of Sugarcrete™, shared his thoughts. "This project has taught us invaluable lessons about how Sugarcrete can enable communities to transition to sustainable building practices," Chandler said. "While we have learned how easy the blocks are to use, we’ve also identified challenges, such as ensuring the availability of materials and skills required for certain lime-based renders."
Early signs are promising. The blocks have performed well through heat, rain, and heavy use. If Sugarcrete™ continues to hold up over the years without crumbling or weakening, it could become a major player in global construction.
The Bigger Picture
One of Sugarcrete’s™ most important features is that it is open access. Anyone with basic manufacturing tools and the right ingredients can make it. That sets it apart from many green technologies, which are often restricted by patents and high production costs.
The Sugarcrete™ team believes this choice decentralizes construction innovation. Instead of waiting for large corporations, small communities, especially in the Global South, can take the lead.
Already, Sugarcrete™ is gaining recognition. It has been nominated for the Earthshot Prize under the "Build a Waste-Free World" category, recommended by past winners Notpla. Researchers at East London also plan to publish several journal papers on the material’s structural, durability, and acoustic properties.
The global impact could be enormous. With two billion tons of sugarcane produced every year, and 600 million tons of bagasse waste, there is no shortage of raw material. In India alone, where 400 million tons of sugarcane are harvested annually, Sugarcrete™ could drive large-scale sustainable development.
"Using only 30 percent of the world bagasse production, Sugarcrete could replace the traditional brick industry entirely, offering a potential saving of 1.08 billion tonnes of CO₂, three percent of the global CO₂ production," the research team emphasized.
Today, the walls of Panchsheel Inter College stand quietly, built from what was once thrown away. But their message speaks loudly: a more sustainable future can rise from the forgotten parts of yesterday.
Note: The article above provided above by The Brighter Side of News.
Like these kind of feel good stories? Get The Brighter Side of News' newsletter.
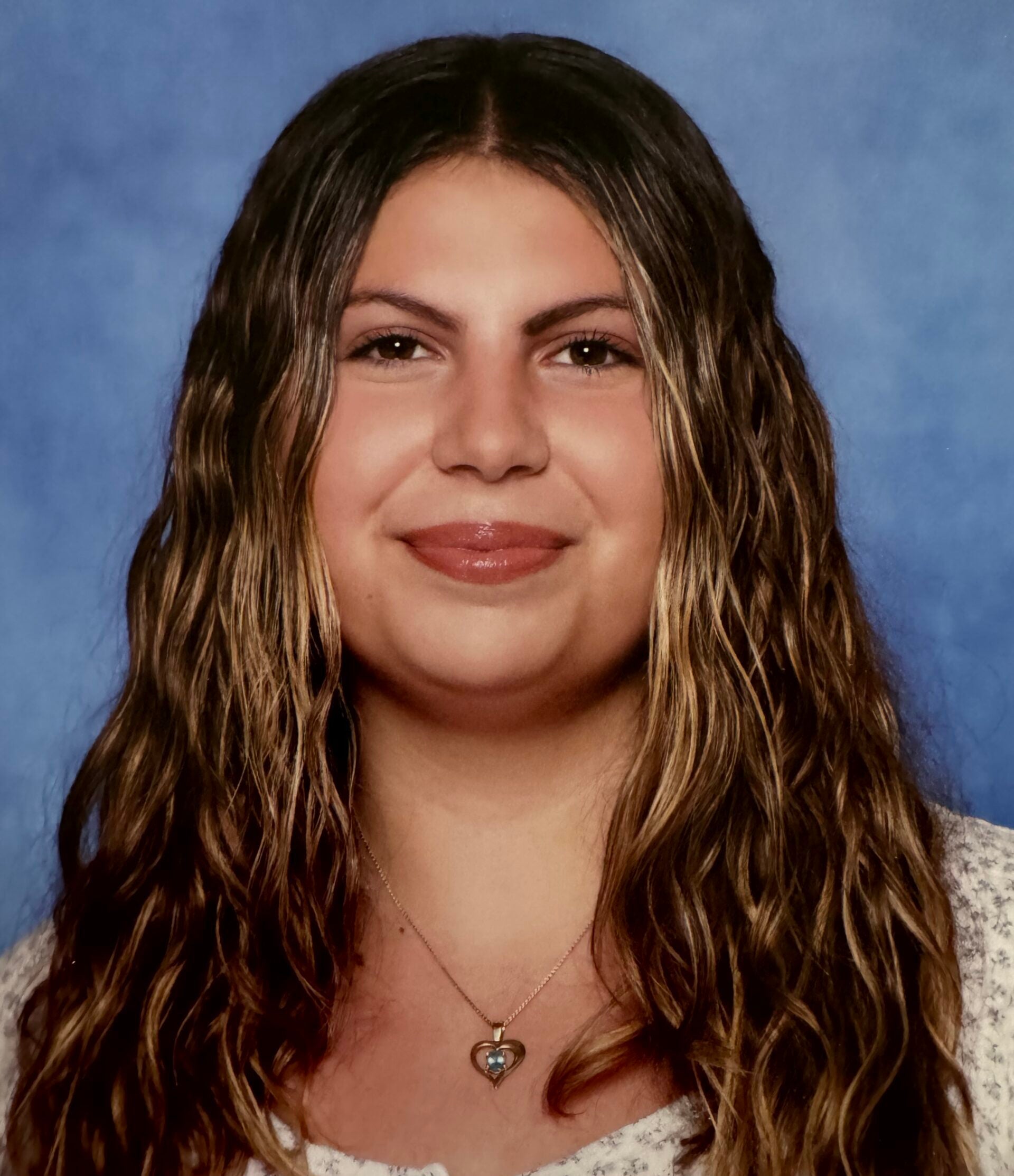
Rebecca Shavit
Science & Technology Journalist | Innovation Storyteller
Based in Los Angeles, Rebecca Shavit is a dedicated science and technology journalist who writes for The Brighter Side of News, an online publication committed to highlighting positive and transformative stories from around the world. With a passion for uncovering groundbreaking discoveries and innovations, she brings to light the scientific advancements shaping a better future. Her reporting spans a wide range of topics, from cutting-edge medical breakthroughs and artificial intelligence to green technology and space exploration. With a keen ability to translate complex concepts into engaging and accessible stories, she makes science and innovation relatable to a broad audience.