Electric vehicles get major boost from new ultra-powerful lightweight battery
By merging battery power with structural strength, researchers are pushing material science in a bold new direction.
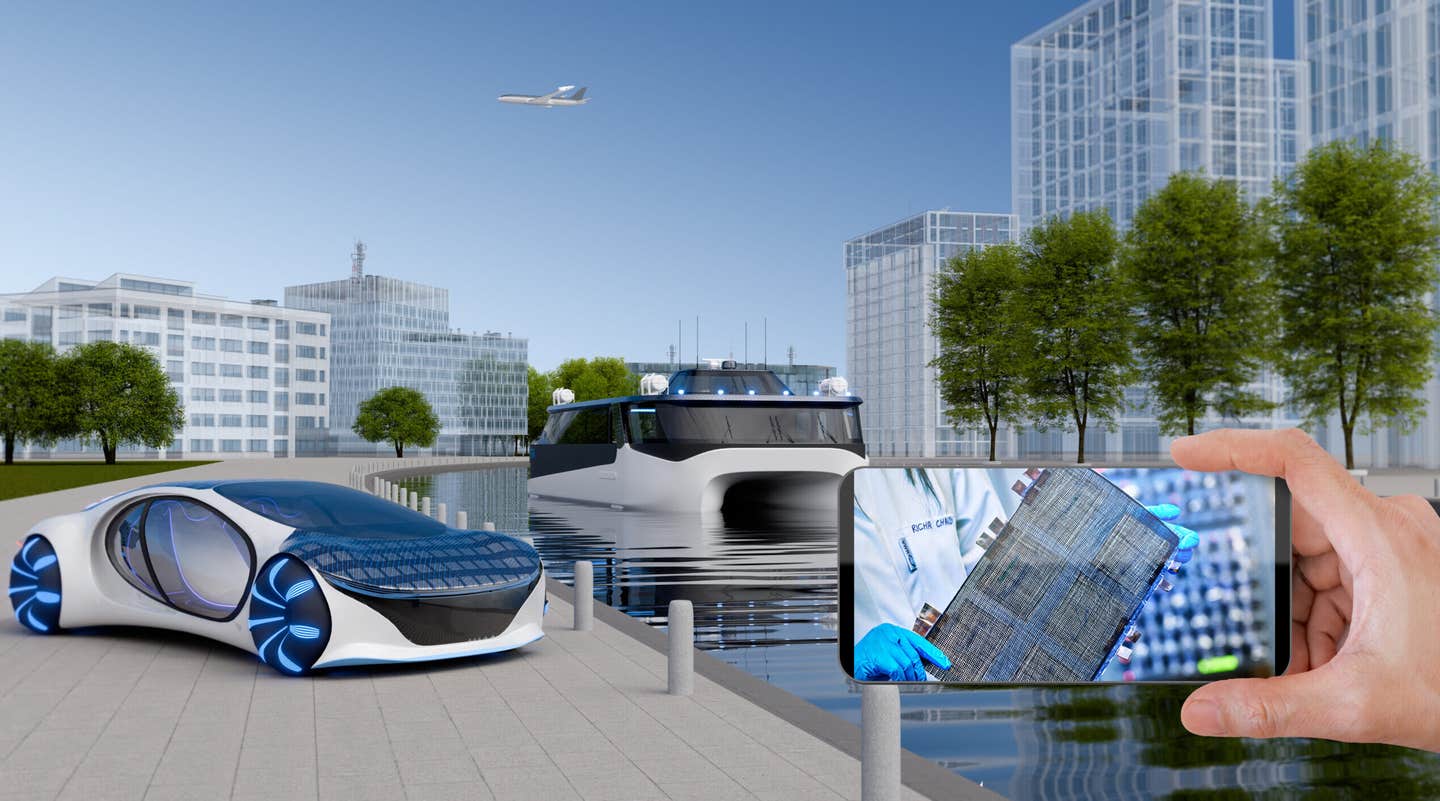
Structural batteries blend energy storage with lightweight design, enabling electric cars to drive farther and devices to become thinner and lighter. (CREDIT: Chalmers University of Technology)
Cutting weight in cars, planes, and gadgets boosts how efficiently they use energy. Traditional lithium-ion batteries, though powerful, have hit a ceiling. Their design limits how much energy can be packed in without adding bulk. This makes it hard to take the next big leap in electric transport or compact devices.
That’s where structural batteries come in. These breakthrough materials don't just store energy—they also support the device's weight. By merging battery power with structural strength, researchers are pushing material science in a bold new direction.
The Concept of Structural Batteries
Unlike regular batteries tucked away in a compartment, structural batteries are part of the frame. They’re built right into the body of the device or vehicle. This design eliminates the need for separate energy and support systems, which slashes overall weight and boosts performance.
Take the roof of an electric car, for example. Swapping it with a structural battery could trim the vehicle’s weight by up to 20%. That saved weight can be used to add more batteries, extending the car’s range and efficiency without increasing its size.
The same idea can reshape how we use personal electronics. A structural battery could cut a laptop’s weight in half or make smartphones almost paper-thin. Electric cars using these batteries might see their driving range jump by as much as 70%.
“It’s like a human skeleton,” says Richa Chaudhary, a researcher at Chalmers University of Technology in Sweden. “It carries loads but also performs other vital functions.” That kind of multifunctional design could change how we think about power and structure in almost every machine.
Related Stories
Materials Driving Innovation
Structural batteries rely on advanced materials like intermediate modulus polyacrylonitrile-based carbon fibers (PAN-CF). These fibers strike the optimal balance between mechanical strength and electrochemical properties, allowing them to act as both electrodes and reinforcement structures.
Recent studies reveal promising results when carbon fibers are coated with lithium iron phosphate (LiFePO₄ or LFP) using electrophoretic deposition. However, initial tests showed poor capacity retention of 47% after 100 cycles due to weak bonding between LFP and carbon fibers.
As LFP nanoparticles detach from the carbon fibers during repeated charging cycles, performance diminishes. By incorporating reduced graphene oxide (rGO) into the design, researchers improved adhesion and achieved a specific capacity of 72 mAh g⁻¹ at a 2C-rate, although this remains below the theoretical potential.
Further innovations include using carbon fibers as the anode and combining them with aluminum foil coated in LFP as the cathode. Testing various separators revealed that thinner materials reduced internal resistance, resulting in higher energy densities. For instance, the Whatman GF plain weave separator outperformed thicker alternatives, doubling energy density from 12 Wh/kg to 24 Wh/kg.
Chalmers University of Technology has been at the forefront of structural battery research. Its groundbreaking work began in 2018, showcasing the ability of stiff carbon fibers to store electrical energy.
The most recent breakthrough saw the creation of a carbon fiber composite battery boasting an energy density of 30 Wh/kg and an elastic modulus of 70 GPa—comparable to aluminum's stiffness but at a fraction of the weight.
As research leader Leif Asp noted, “Investing in light and energy-efficient vehicles is a matter of course if we are to economize on energy and think about future generations.” With these advancements, structural batteries could make electric cars 70% more energy-efficient while meeting strict safety standards.
Advancing Towards Commercialization
The journey from lab to market is challenging but increasingly promising. The Chalmers team has formed Sinonus AB to accelerate commercialization. Applications in portable electronics, such as credit card-thin smartphones or ultra-light laptops, may be the first to benefit. In the long term, this technology could revolutionize aerospace and automotive industries.
However, significant engineering hurdles remain. For instance, transitioning from liquid to semi-solid electrolytes is critical for achieving higher power densities and improved safety. Semi-solid electrolytes reduce fire risks, an important factor in commercial adoption.
Structural batteries offer several environmental benefits. By eliminating the need for heavy current collectors made of aluminum or copper, these batteries reduce material usage. Additionally, their design avoids conflict metals like cobalt, frequently associated with traditional lithium-ion batteries.
The integration of carbon fibers into both electrodes simplifies the overall structure, further lowering weight. In the anode, the fibers act as reinforcement, current collectors, and active material. In the cathode, they support lithium deposition, eliminating unnecessary components and streamlining production.
Challenges and Future Directions
Despite significant progress, challenges remain. Liquid electrolytes currently dominate research, limiting the structural battery's full potential. Additionally, using carbon fibers exclusively as negative electrodes or relying on commercial LFP foils for positive electrodes restricts innovation.
Addressing these limitations, Chalmers researchers recently demonstrated an all-carbon-fiber structural battery using pristine carbon fibers as the anode and LFP-coated fibers as the cathode. Embedded in a biphasic solid-liquid electrolyte system, this design achieved an energy density of 33.4 Wh/kg, with an impressive Young's modulus of 38 GPa.
Improvements in manufacturing techniques have further increased energy density to 42 Wh/kg while maintaining mechanical robustness. These advances underline the potential for structural batteries to integrate seamlessly into large-scale industrial applications, such as cars, planes, and drones.
The global interest in structural batteries is growing, particularly within the automotive and aerospace sectors. These industries stand to benefit the most from lighter, more energy-efficient designs. However, significant investments in research and manufacturing are needed to meet the energy demands of these sectors.
As Professor Asp points out, “One can imagine that credit card-thin mobile phones or laptops that weigh half as much as today are the closest in time.” With structural batteries poised to disrupt the status quo, the dream of multifunctional materials driving our vehicles, powering our gadgets, and reducing environmental impact may soon become reality.
Note: Materials provided above by The Brighter Side of News. Content may be edited for style and length.
Like these kind of feel good stories? Get The Brighter Side of News' newsletter.
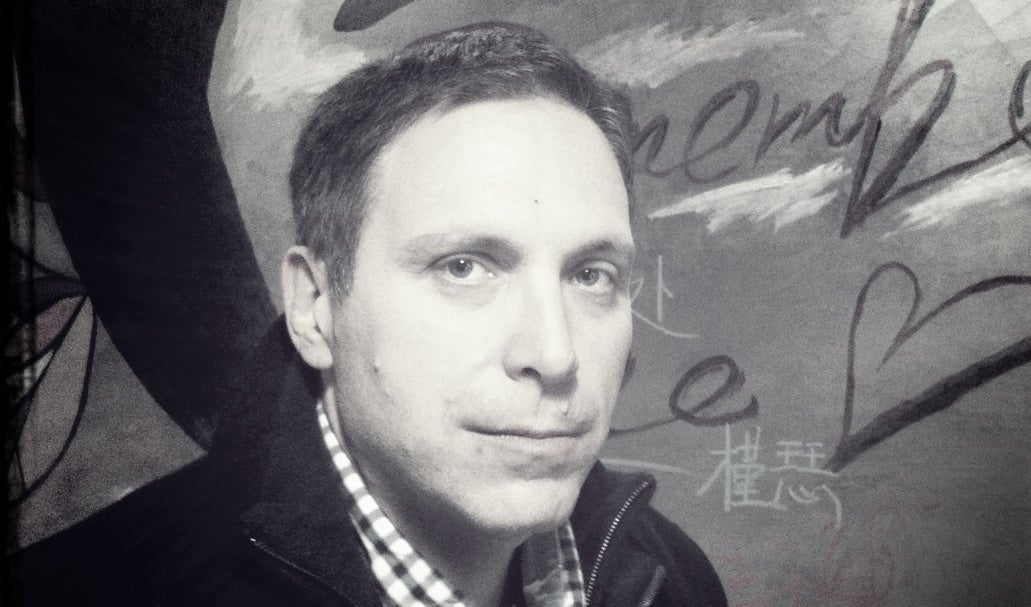
Joseph Shavit
Head Science News Writer | Communicating Innovation & Discovery
Based in Los Angeles, Joseph Shavit is an accomplished science journalist, head science news writer and co-founder at The Brighter Side of News, where he translates cutting-edge discoveries into compelling stories for a broad audience. With a strong background spanning science, business, product management, media leadership, and entrepreneurship, Joseph brings a unique perspective to science communication. His expertise allows him to uncover the intersection of technological advancements and market potential, shedding light on how groundbreaking research evolves into transformative products and industries.